Manual One Arm Wheelchair
This project was completed in partnership with The Ohio State University Wexner Medical Center while working on an interdisciplinary engineering team. The project was to develop an alternative manual wheelchair that can be operated with only one arm.
The design centered around using a single lever that added forward propulsion when pushing and pulling. The lever also allowed for joystick-like turning by leaning it to the left or the right. Finally, braking was accomplished by a familiar hand brake.

Establishing a Need
The device will most commonly be used by people that have one-sided muscle weakness (hemiparesis). This impairment is a side effect of a traumatic brain injury, cerebral palsy, and most commonly a stroke.
​
In the United States:
-
795,000 people suffer from a stroke each year
-
78% of stroke patients experience hemiparesis
-
75% of stroke patients with hemiparesis remain chronically effected by it
​
...meaning ~465,000 people annually are in need of a long term assisted mobility solution due to strokes alone.
Why Design an Alternative?
At the time of the project, the two available options were the "dual handrim" manual wheelchair or a joystick operated electric wheelchair. After interviewing patients about their experiences and trying out both devices for ourselves, it became very clear why the medical center posted this project.
​
In the short term, electrically powered wheelchairs require a level of cognitive awareness that recovering stroke patients do not have. Over the long term, patients expressed the feeling of being "tied down" or restricted due to the difficulty of transporting an electric chair and the high-cost barrier.
​
The only single arm operated manual wheelchair design on the market functions as advertised, but is unusable in practice. The controls are intuitive and require an immense amount of strength and dexterity to operate properly; healthy college students struggled to generate any sustained motion or accurate maneuverability.
​
This impracticality and unsuitability of both options have led the OSU medical professionals to prescribe normal wheelchairs in lieu of the intended options. Patients will use their strong arm to operate one wheel and their strong leg to pull on the floor to assist movement and turning.

Dual Handrim
+ Collapsible
+ Light Weight
+ Maintain User Independence
​
- Extreme fatigue
- Poor maneuverability
- Unintuitive

Electric
+ Minimal Physical Requirement
​
- Large and Heavy
- Hard to Transport
- Expensive
Early Brainstorming
The team started by individually sketching concepts for different subsystems such as turning, braking, propulsion, and rehabilitation attachments.
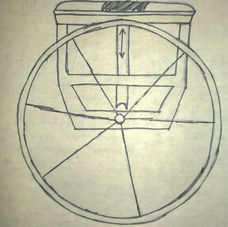
These concepts were then distilled down to develop four different concepts:
​
-
Lever with dual propulsion drive
-
Single axel, with slide to turn
-
Caster Handrim
-
Big bar drive mechanism
​
The team then built conceptual prototypes to help visualize the motions required to operate the design.



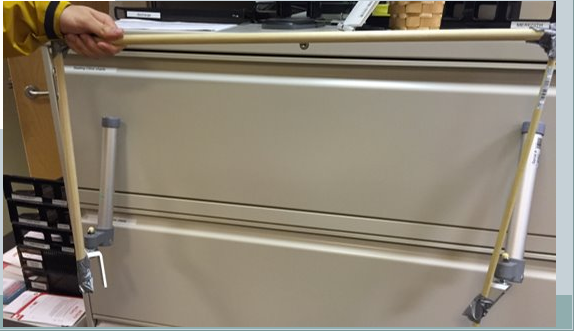
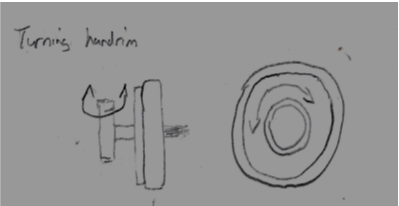
In order to select a design to proceed with, the group identified criteria to evaluate each design and assigned each category a weight based on the information gathered during our research phase.
​
By prioritizing categories, the team was able to identify the concept that best embodies the most important features.
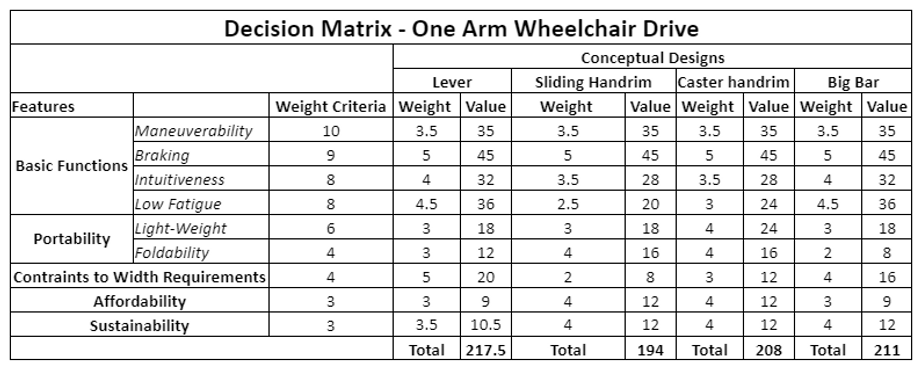
From the decision matrix, the team selected the Dual Propulsion Lever Drive concept to move forward with.
​
Before moving on with the build, the team collectively sketched out holistic concepts that depicted all of the features of the design. This allowed us to identify a general layout for the chair and understand how all of the subsystems will interact with each other. From there, responsibilities for the different subsystems were delegated amongst the team members.

Features
Lever
-
A standard bike brake handle will be attached to the top to actuate the brakes.
-
In order to turn, the top portion of the lever will pivot left and right to actuate the brakes on only one side of the chair.
-
A magnetic contact will keep the lever centered when not turning.
​
Drive Train
-
Forward motion will be added when the lever is pushed and pulled to maintain momentum, what we call "Dual Drive".
-
The lever axle will connect to a differential on the rear axle using a chain and sprocket.
​
Braking
-
Each side of the rear axle will be equipped with a rotor and caliper brake with cables running up to the handle.

Delegation
The design was divided into four main areas and each assigned to a different team member as the owner to ensure the component was completed.
​
-
Lever
-
Dual Drive Functionality
-
Braking
-
Drive Train
​
Initially, I was the team member to develop the concept for the Dual Drive functionality, so I selected to be the owner of that subsystem.
Dual Drive Mechanism
The design was refined down from the earlier concept to a more compact form.
​
The whole assembly is suspended using two brackets that are attached to the wheelchair frame on the underside of the seat.
​
Starting on the right, the grey hub connects to the lever (not shown).
​
Inside of the hub, the pink and cyan objects are standard roller clutches that operate similarly to a ratchet, but without the noise. They are oriented to freely rotate in opposite directions in order to transfer force when the lever is pushed and pulled.
​
The red tube is the main axle for the forward push of the lever and connects directly to the custom hub in the center.
​
The green tubes are the main axle for the backward pull of the lever. The challenge is that rotation applied from the lever needs to be reversed to create the dual drive motion. To accomplish this, the axle is separated and attached to bevel gears (shown in gold). These gears have a 1:1 ratio so no torque is lost; they only reverse the rotation.

The team was given a timeline of 5 weeks and a budget of $1,000 in order to purchase all of the parts and raw materials and complete the build phase. The concept is intended to be an "add on" kit to any existing wheelchair, so the team was provided with a standard wheelchair to work with.
​
All of the custom machining and modifications were performed by myself and two other team members.
​
At the end of the build phase, the team successfully completed a proof of concept prototype.
Future Development
The main issue is the drive train would lock up when a user was in the chair. In order to remedy this the team identified the following:
​
-
Incorporate thrust bearings into the mounting brackets to counter the axial loading from the bevel gears.
-
Design a sturdier mounting solution for the bevel gears.
-
Integrate a tensioner to reduce the slack in the chain.
-
Angle the resting position of the handle and lever to a more ergonomic position.
-
Incorporate a solution to allow the chair to move in reverse.
-
Incorporate a solution to allow the chair to go into neutral if someone is pushing.
